Contacts
Chemical mille contacts, connectors, terminals, and bus bars are essential components used in electrical and electronic systems for reliable electrical connections
Different manufacturing processes are selected based on the material, design complexity, volume requirements, and desired properties of the final component. Chemical Milling is favored for high precision and complex designs, while stamping are used for high-volume production of simpler shapes. Each method offers unique advantages depending on the specific needs of the application
However Chemical Milling to achieve high precision and intricate designs. Here’s an overview of these components, including materials, typical thicknesses, and applications
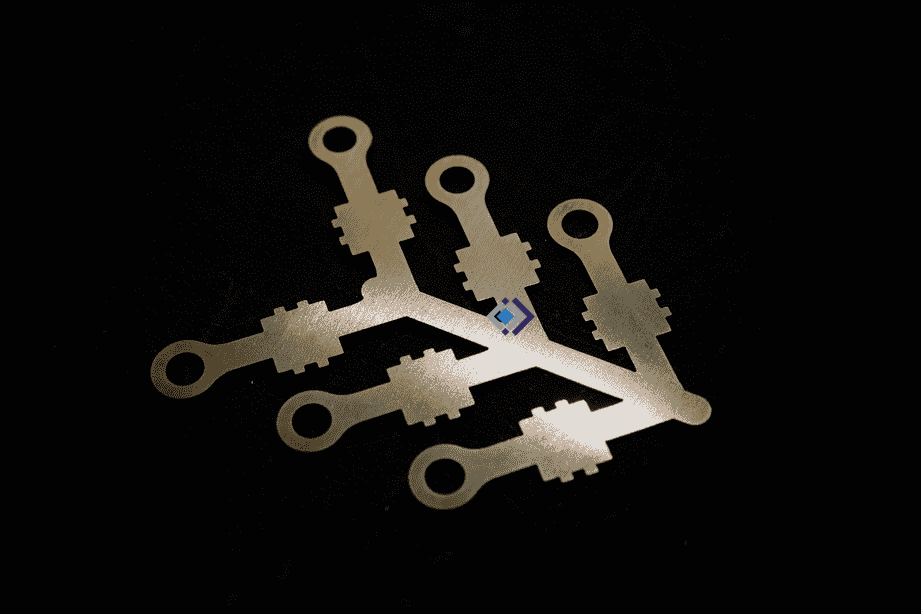
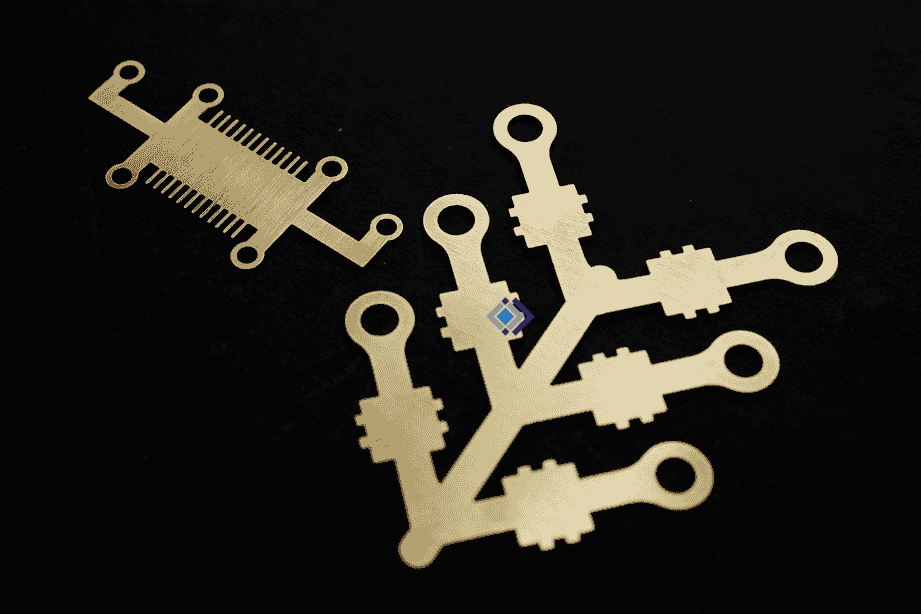
Typical Thickness Range:
Generally range from 0.05 mm to 0.3 mm. The thickness depends on the application, electrical requirements, and mechanical strength needed.
Customization:
Usually thicker, ranging from 0.3 mm to 3 mm depending on the current-carrying requirements and the design of the bus bar.
Material We Used
Copper
Copper Alloys
Stainless Steel
Nickel & Nickel Alloys
Advantage of
CHEMICL MILLED Components
High Precision:
Chemical Milling allows for the production of components with intricate designs and tight tolerances, which is crucial for reliable electrical connections.
Customizability:
The process enables the creation of custom shapes and sizes to meet specific application requirements.
Consistency:
Ensures uniformity and reliability across large production runs.
Reduced Waste:
Minimizes material waste compared to traditional machining methods.
Versatility:
Suitable for a wide range of materials and applications, including those requiring high precision and complex
geometries.